Working principle and installation method of motor bearing
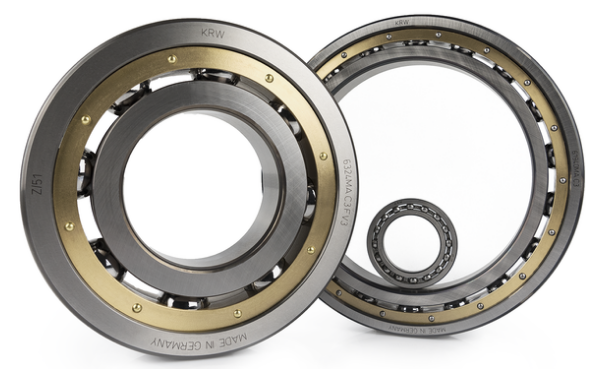
Motor bearing, also known as motor bearing or motor bearing, is a special bearing specially used in electric motors or motors. The bearing used in the motor is a part that supports the shaft, it can guide the rotation of the shaft, and it can also bear the part that is idling on the shaft. There are four types of bearings commonly used in motors, namely rolling bearings, sliding bearings, spherical plain bearings and oil-impregnated bearings. The most common motor bearings are rolling bearings, ie bearings with rolling elements.
1. Working principle:
Motor bearings utilize smooth metal balls or rollers and lubricated inner and outer ring metal surfaces to reduce friction. These balls or rollers “carry” the load and support the motor shaft, allowing the motor (rotor) to rotate smoothly.
Second, the bearing type:
Most small and medium motors use rolling bearings. Large and medium size motors also use rolling bearings. The bearings at both ends of the small motor use ball bearings (such as deep groove ball bearings). Medium-sized motors use roller bearings at the load end (such as cylindrical roller bearings, tapered roller bearings. Generally used for high-load conditions), and use ball bearings at the non-load end (but there are also opposite cases, such as 1050kW motors). Rolling bearings are lubricated with grease, but also lubricated with lubricating oil.
3. Bearing installation:
Whether the motor bearing is installed or not will directly affect the accuracy, life and performance of the bearing. Therefore, please fully study the bearing installation, that is, please install the motor bearing according to the operating standards including the following items.
- Clean the motor bearings and related parts, (oil seals or dust caps are provided for grease-lubricated bearings and both sides, and there is no need to clean the bearings with seal rings before installing them.)
- Check the dimensions and finishing conditions of related parts
Fourth, the installation method
The installation of the motor bearing should be determined according to the bearing structure, size and the matching nature of the bearing components. The pressure should be directly applied to the end face of the ferrule with a tight fit, and the pressure should not be transmitted through the rolling elements. The installation of the motor bearing generally adopts the following methods:
1. Press fit
When the inner ring of the motor bearing is tightly fitted with the shaft, and the outer ring and the bearing seat hole are loosely fitted, the motor bearing can be press-fitted on the shaft first, and then the shaft together with the bearing is installed into the bearing seat hole, and then press-fitted. When the motor bearing inner ring end face, pad a soft metal material assembly sleeve (copper or mild steel).
The outer ring of the motor bearing is tightly fitted with the bearing seat hole, and when the inner ring and the shaft are loosely fitted, the motor bearing can be pressed into the bearing seat hole first. At this time, the outer diameter of the assembly sleeve should be slightly smaller than the diameter of the seat hole.
If the bearing ring of the motor is tightly fitted with the shaft and the seat hole, the inner ring and the outer ring should be pressed into the shaft and the seat hole at the same time during installation, and the structure of the assembly sleeve should be able to press the end faces of the inner ring and the outer ring of the bearing at the same time.
2. Heating coordination
A mounting method that uses thermal expansion to convert a tight fit into a loose fit by heating the motor bearing or housing. It is a common and labor-saving installation method. This method is suitable for the installation of motor bearings with large interference. Before hot-fitting, put the motor bearing or the ferrule of the separable bearing into the oil tank and evenly heat it at 80-100°C, then take it out of the oil and install it on the shaft as soon as possible. , In order to prevent the inner ring end face and the shaft shoulder from not fitting tightly after cooling, the motor bearing can be axially tightened after cooling. When the outer ring of the motor bearing is tightly fitted with the bearing seat made of light metal, the hot-fitting method of heating the bearing seat can be used to prevent the mating surface from being scratched.
When heating the motor bearing with the oil tank, there should be a mesh grid at a certain distance from the bottom of the box, or use a hook to hang the motor bearing. The motor bearing cannot be placed on the bottom of the box to prevent heavy impurities from entering the motor bearing or uneven heating. There must be a thermometer, and the oil temperature should not exceed 100 ℃ strictly to prevent the tempering effect and reduce the hardness of the ferrule.
Fault analysis and treatment of abnormal sound of motor bearing
1. Abnormal sound of motor bearing
A feed pump high-voltage (6kV) motor YKK400-2, power 450kW, speed 2975r/min, shaft extension end uses deep groove column NU3E222 type bearing, non-load end uses deep groove ball 6222 type bearing. During operation, the sound of the shaft extension end is sharp and ear-piercing, not like electromagnetic noise, nor like the sound of dry grinding due to lack of oil in the bearing. The noise lasts for about 2 minutes, and then intermittently for 2 minutes. Use a vibration meter (VA-80A) to measure the vibration amplitude of the bearing. The value is 0, 021mm, when the sound is abnormal, the measured vibration speed value is 53, 6m/s, and sometimes even reaches 97m/s, far exceeding the standard value of 28m/s, and the current fluctuates greatly.
Due to the clearance fit at the shaft extension, the axial positioning dimension of the bearing cannot be adjusted. During the maintenance process, it was found that the inner oil cover had uneven wear marks, and the bearing had two deep groove column damage. Measure the positioning dimensions of the bearing, the end cover and the inner and outer oil baffles, and after calculation, the allowable clearance of the bearing is 0.7mm. When the bearing temperature of the motor reaches 100 °C, the expansion value of the bearing is about 0.9mm, which cannot meet the normal requirements of the motor. run requirements. After replacing the deep groove column bearing many times, the motor noise not only did not disappear, but the abnormal sound period became 4min.
2. Failure analysis and handling
Analysis according to the characteristics of the bearing: Since the motor originally used NU type deep groove column bearing, the motor is allowed to move axially. The inner ring of the bearing has ribs on both sides, and the outer ring has no ribs, so the shaft is allowed to move in two directions relative to the bearing, and can withstand the elongation caused by the thermal expansion of the shaft. At the same time, the clearance of the bearing is larger than that of the deep groove ball bearing, but the force of the bearing is linear, which is better than the point force of the deep groove ball bearing. The bearing movement trajectory is not a circle but an ellipse, which is caused by the gap between the dry deep groove column (or deep groove ball) and the raceway, and the different forces during operation make the movement trajectory an ellipse. The force of the bearing is mainly in the lower part. For the deep groove column bearing, the force point is a straight line. During high-speed operation, due to the clearance of the bearing, the force point changes, and the force trajectory becomes a parabolic curve.
When the feed pump motor is running, it is mainly affected by the axial force, and the dragging load is stable, and the necessity of the radial movement allowed by the deep groove column bearing is weakened. Therefore, the front bearing is replaced with a deep groove ball bearing, and the bearing clearance is still C3 , about 0, 04mm, can meet the operating requirements. At the same time, considering the expansion of the bearing, a gasket with a thickness of about 0.8mm is added to the small cover of the oil slinger to overcome the turbulence caused by the temperature rise of the feed water pump and the bearing.
The microscopic surface curvature of the bearing rolling element and raceway is rough and uneven, and a certain impact will occur during the movement, but the pulse generated by this impact is high frequency, so the vibration meter is used to measure the parameter value of the high frequency interference of the motor operation. bigger than standard. The deep groove cylindrical bearing has more contact with the raceway, and the resulting high-frequency impact is large, while the contact between the deep groove ball bearing and the raceway is a point, and the high-frequency impact generated is relatively small, so the motor in this example can use deep grooves. The groove ball bearing replaces the deep groove column bearing to solve the abnormal noise of the equipment.
After replacing the deep groove column bearing with a deep groove ball bearing, the abnormal noise of the bearing disappeared. After running for a period of time, the noise did not appear again. The vibration amplitude of the motor was measured as 0.013mm, and the acceleration value was 2.8m/s2. The load performance was stable, and the current did not fluctuate greatly.