Learning the Basics of Supply Chain Planning
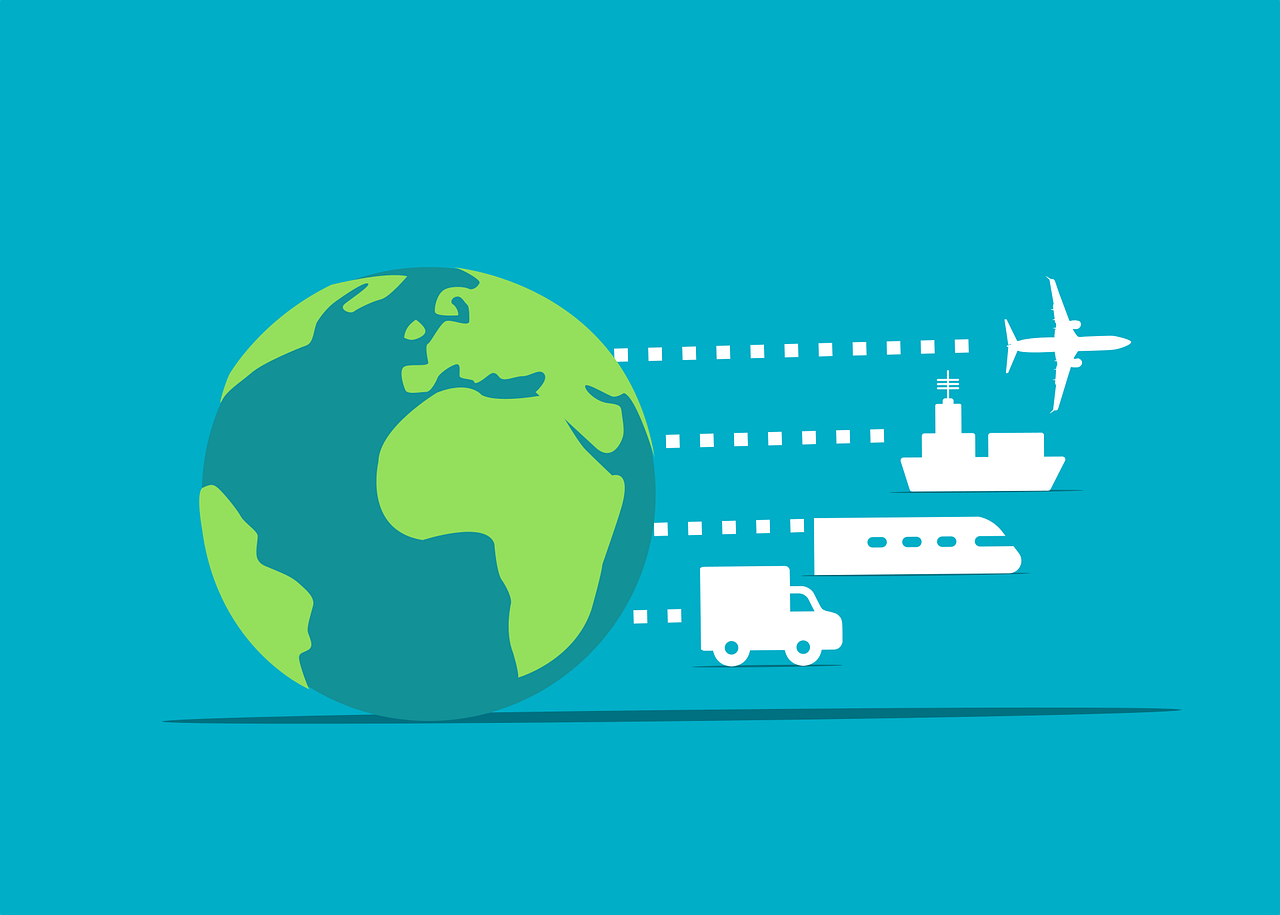
Supply chain planning is an essential part of any business. It’s the process by which a company manages its various stock levels, logistics, and orders to ensure that goods and services are delivered on time. Without proper supply chain planning, companies will struggle with inventory management, delays in deliveries, and customer dissatisfaction. For businesses looking to make sure their operations are running as smoothly and efficiently as possible, understanding the basics of supply chain planning is key. In this blog post, we’ll take a look at what supply chain planning entails and the tools available for managing it. Read on to learn more about how you can implement an effective supply chain plan for your business.
What is Supply Chain Planning?
Supply chain planning is the process of coordinating and managing all the activities that go into moving goods from suppliers to customers. It includes everything from sourcing raw materials to manufacturing products to distributing them to retailers. The goal of supply chain planning is to ensure that goods are produced and delivered in a timely, efficient, and cost-effective manner.
Most businesses use some form of supply chain planning, whether they’re aware of it or not. Even if a company doesn’t have a dedicated supply chain department, someone is likely overseeing the various moving parts and ensuring that everything runs smoothly.
There are many different software programs and tools available to help with supply chain planning. Some companies opt for comprehensive enterprise resource planning (ERP) systems that include supply chain management functionality. Others use more specialized supply chain planning software. There is no one-size-fits-all solution; the best software for your business will depend on your specific needs and goals.
Read More: DYNAMICS 365 DRIVES IMPROVEMENT IN MANUFACTURING SUPPLY CHAINS
If you’re new to supply chain planning, or if you’re considering implementing a new system, it’s important to have a clear understanding of the basics before you get started. This guide will teach you the essentials of supply chain planning, including what it is, why it’s important, and how to get started
The Benefits of Supply Chain Operation Planning
Supply chain planning is a process used by organizations to manage the execution of their supply chain operations. The goal of supply chain planning is to optimize the flow of goods and materials throughout the supply chain, from suppliers to customers.
There are many benefits of supply chain planning, including:
- improved customer satisfaction – when done correctly, supply chain planning can help ensure that customers receive the products they need, when they need them. This can lead to increased customer satisfaction and loyalty.
- increased efficiency – a well-planned supply chain can help organizations reduce waste and increase efficiency in their operations. This can lead to cost savings and improved profitability.
- reduced risk – proper planning can help organizations avoid disruptions in their supply chains, which can lead to costly delays and lost sales. Supply chain planning can also help organizations respond quickly and effectively to unexpected events, such as natural disasters or economic downturns.
- improved competitiveness – a well-run supply chain can give organizations a competitive advantage over their rivals. A strong supply chain can help businesses keep up with demand, launch new products quickly, and adapt to changes in the marketplace.
The Different Types of Supply Chain Plans
There are a variety of different types of supply chain plans that can be used to guide decision-making and operations within a company. The most common types of plans include production plans, inventory plans, transportation plans, and distribution plans.
Production plans detail the specific steps that need to be taken in order to produce a product or service. This type of plan typically includes information on manufacturing processes, input and output levels, quality control procedures, and other aspects of production.
Inventory plans focus on managing the levels of raw materials, finished goods, and work-in-progress inventory. This type of plan includes information on stock levels, lead times, reordering points, and safety stock levels.
Transportation plans outline the routes and schedules that will be used to move goods from one location to another. This type of plan typically includes information on mode of transport (e.g., rail, truck, ship), transit times, shipping costs, and capacity constraints.
Distribution plans detail the methods that will be used to get products from the point of manufacture to the point of sale. This type of plan typically includes information on warehousing strategies, order fulfillment processes, delivery schedules, and customer service procedures.
Developing a Supply Chain Plan
In order to develop an effective supply chain plan, businesses need to first understand the basics of how supply chains work. By understanding the different components of a supply chain and how they interact with one another, businesses can develop a plan that will optimize their operations and minimize costs.
The first step in developing a supply chain plan is to understand the various components of a supply chain. A supply chain is made up of four main components: suppliers, manufacturers, distributors, and retailers. Each component has its own set of activities and tasks that need to be coordinated in order for the entire system to run smoothly.
The second step in developing a supply chain plan is to identify the specific needs of your business. What are your company’s goals? What are your customers’ needs? Once you have a clear understanding of your business’s needs, you can begin to develop a plan that will meet those needs.
The third step in developing a supply chain plan is to create a timeline for implementing your plan. You’ll need to consider the lead time for each component of your supply chain and make sure that your timeline takes into account any seasonality or other factors that could impact production or delivery.
The fourth step in developing a supply chain plan is to create a budget for your project. Be sure to consider all the costs associated with each stage of your supply chain, from raw materials to finished products. Once you have a budget in place, you can begin to look for ways to optimize
Implementing a Supply Chain Plan
After you’ve designed your supply chain, it’s time to implement your plan. This is where the rubber meets the road, and where you can start to see the benefits of your hard work.
There are a few things to keep in mind when implementing your supply chain plan:
- Make sure you have buy-in from all stakeholders. Your supply chain won’t work if everyone isn’t on board.
- Be realistic about what can be accomplished in the short-term and long-term. Don’t try to do too much too soon – you’ll just get frustrated. Start small and build on successes.
- Have a clear understanding of your data and what it tells you about your business. This data will be the foundation of your decision-making, so make sure it’s accurate and actionable.
- Use technology to automate as much as possible. Technology can help you streamline processes and make your life easier. But don’t rely on it completely – use it as a supplement to good old-fashioned hard work.
- Finally, always be prepared to adapt as the market or your business changes. The best-laid plans often go awry, so be flexible and be ready to adjust course when necessary.”
Evaluating the Success of a Supply Chain Plan
Evaluating the success of a supply chain plan can be a complex undertaking, as there are many factors to consider. However, by keeping a few key points in mind, it is possible to get a good sense of how successful your plan has been.
- Look at the big picture: It is important to remember that supply chain planning is just one part of the larger puzzle of running a business. As such, it is important to look at how your plan fits into the overall strategy and objectives of your company. If your supply chain plan is not aligned with these broader goals, it is likely that it will not be successful.
- Consider all stakeholders: A successful supply chain plan must take into account the needs of all stakeholders involved. This includes suppliers, customers, logistics providers, and other partners. If any of these groups are not being considered properly, it will likely impact the success of your plan.
- Track metrics: There are a number of metrics that can be used to track the success of a supply chain plan. These include things like on-time delivery rates, fill rates, inventory levels, and costs. By tracking these metrics over time, you can get a good sense of how well your plan is performing.
- Make adjustments: Even the best-laid plans will need to be adjusted from time to time based on changes in the market or business environment. Be prepared to make changes to your supply chain plan as needed
Conclusion
In conclusion, supply chain planning is a critical component of any business strategy. It helps ensure that you are sourcing the right inventory at the best prices and provides insight into customer demand. By understanding the basics of supply chain planning, you can make better decisions about how to optimize your operations and reduce costs while still providing customers with quality products and services. As you continue to refine your strategies in this area, you will be able to create a more efficient supply chain that delivers maximum value for all stakeholders involved.